Dedusting systems
General
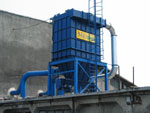
Dedusting is carried out by efficient bag filters with pulse jet cleaning of bags or by cartridge filters .

For prevention of secondary dusting upon discharging of dust deposed in filter hopper, a water spraying devices are provided as well as conveyor systems with water and vapor moistening.
In some cases, when dedusting systems are a part of a complete production line, an entirely dustless technologies are applied.
At client’s request, the control of dedusting plants can be manual, remote or fully automatic. The last one is performed through dust collector controllers upon preset algorithm. They control the normal state of equipment units and technological parameters as well perform high level commands.
Application
Technological gases from production, dressing and sintering plants, metallurgical units, bunker gantries for raw materials, transloading sections, crushers, screens etc.
Technological gases from cupola, induction and resistance furnaces, sand and moulding workshops, shaking grids etc. | ![]() |
Technological equipment and belt conveyors for transportation of raw materials and final products | ![]() |
Power stations - transloading sections, transport lines for coil and ash, steam boilers |
![]() ![]() |
Cement and lime furnaces, crushers, sieves, transport lines for raw materials and final products |
![]() |
Dust laden air flows, separated during ceramic and faience processing as well as production of tiles and bricks |
![]() |
Dry dedusting of gases, separated from asphalt plants drum mixers |
![]() ![]() |
Local aspiration of woodworking machines |
![]() |
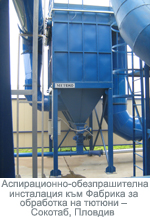
Unloading stations for pneumatic-transport systems | ![]() |